Running a warehouse in Malaysia isn’t just about having a big space to store goods—it’s about managing a multitude of hidden costs that can quickly eat into your profits if not properly addressed. In today’s competitive market, achieving operational efficiency is key to staying profitable. Let’s dive into the often-overlooked expenses and explore smart strategies to keep costs under control while boosting your bottom line.
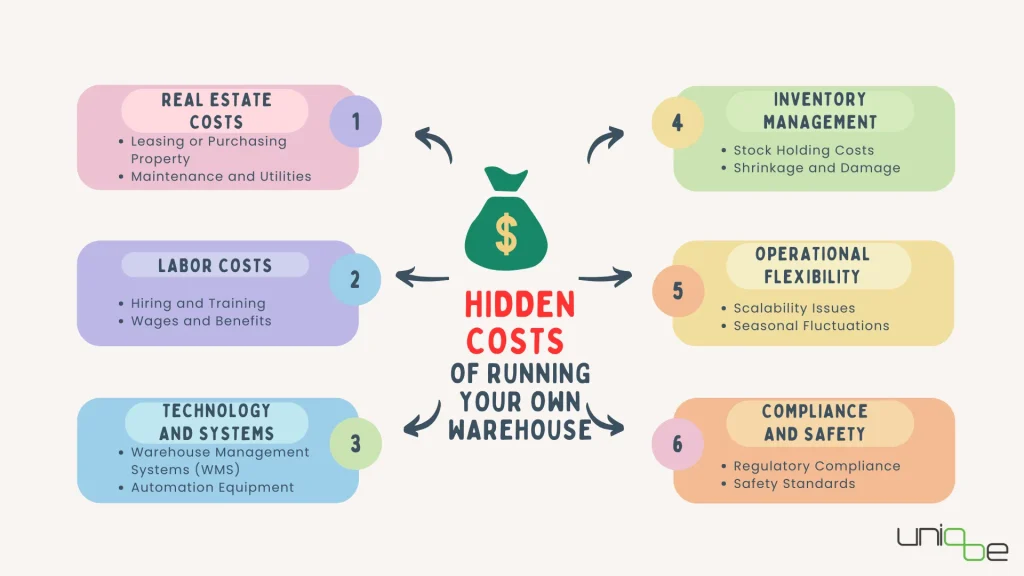
Identifying Hidden Costs
When you’re managing a warehouse, several hidden costs might be lurking around the corner:
1. Real Estate Costs
- Leasing or Purchasing Property: Acquiring space for a warehouse involves significant upfront investment. This includes either leasing or buying property, which can vary greatly depending on the location and size.
- Maintenance and Utilities: Beyond the initial investment, ongoing costs for maintenance, utilities, and property taxes can be substantial.
2. Labor Costs
- Hiring and Training: Recruiting skilled workers and providing necessary training is a recurring expense. Additionally, high turnover rates in warehouse jobs can lead to continuous recruitment and training cycles.
- Wages and Benefits: Competitive wages, healthcare, and other benefits for warehouse staff add to the overall labor costs.
3. Hidden Costs in Technology and Systems
- Warehouse Management Systems (WMS): Implementing and maintaining a robust WMS is crucial for efficient operations. This involves software costs, upgrades, and IT support.
- Automation Equipment: Investing in automation tools such as conveyors, robotics, and barcode systems requires significant capital and ongoing maintenance.
4. Inventory Management
- Stock Holding Costs: Keeping inventory in-house means bearing the costs of storage, insurance, and potential obsolescence.
- Shrinkage and Damage: Losses due to theft, damage, or mismanagement add hidden costs that can impact profitability.
5. Operational Flexibility
- Scalability Issues: As your business grows, scaling your warehousing operations can be challenging and expensive. This includes expanding physical space and adjusting staffing levels.
- Seasonal Fluctuations: Managing peak seasons requires temporary labor and additional resources, leading to increased costs during high-demand periods.
How 8Stock helps Malaysian company to Reduce Operational Costs of a Warehouse
6. Hidden Costs in Compliance and Safety
- Regulatory Compliance: Ensuring compliance with local, state, and federal regulations requires regular updates and can lead to fines if not properly managed.
- Safety Standards: Implementing and maintaining safety standards to protect workers and inventory involves training and equipment costs.
Strategies for Cost Mitigation of the Hidden Costs
Now that we’ve pinpointed where your money might be disappearing, let’s explore some effective strategies to mitigate these costs:
- Implementing Smart Warehouse Technologies: Automation, advanced WMS, and robotics can transform your warehouse operations. These technologies help in streamlining processes, reducing human errors, and ultimately achieving efficient warehouse management in Malaysia.
- Outsourcing to 3PL Providers: Third-party logistics (3PL) providers offer an excellent way to reduce capital investments while providing scalability and flexibility. Outsourcing can ease the financial burden of owning and maintaining your own warehouse.
Optimizing Inventory Management: Adopting modern inventory management techniques can help cut down on stock holding expenses, reduce shrinkage, and minimize damages. A well-organized system ensures you only pay for what you truly need.
Benefits Implementing Smart Warehouse Technologies
Investing in smart warehouse technologies not only cuts costs but also brings several other benefits:
- Increased Efficiency: By reducing manual errors and automating routine tasks, your warehouse can operate more smoothly, leading to a noticeable boost in productivity.
- Enhanced Customer Satisfaction: With faster order fulfillment and accurate deliveries, your customers are more likely to be happy and loyal to your brand.
- Improved Safety: Automation and modern safety systems can significantly lower the risk of accidents, creating a safer working environment for everyone.
Read 8Stock’s article on How Smart Warehouse Streamline Warehouse Operations and Boost Efficiency
The Benefits of Outsourcing to a 3PL Provider
Outsourcing to a 3PL provider near you can mitigate many of these hidden costs, such as:
- Cost Savings: Reduced need for capital investment in real estate, technology, and labor.
- Expertise and Efficiency: Leveraging the expertise of 3PLs in logistics and supply chain management.
- Scalability: Easier adjustment to fluctuating demand and business growth.
- Focus on Core Business: Allowing your business to concentrate on what it does best, leaving logistics to the experts.
Case Studies and Examples
A great way to understand these benefits is by looking at real-life examples. Companies like Mr. DIY Malaysia have successfully adopted smart warehouse practices to streamline their operations. While there are challenges—such as the high initial cost of technology adoption versus ongoing labor costs—the long-term savings and operational improvements often outweigh these hurdles. These case studies offer valuable insights into the tangible benefits of modernizing warehouse operations.
Conclusion
While managing your own warehouse might seem like a good idea initially, the hidden costs can be overwhelming. Outsourcing to a 3PL provider not only helps in reducing these costs but also brings in expertise, efficiency, and scalability to your business operations. Make an informed decision by considering all the hidden costs associated with running your own warehousing and fulfillment operations.