Efficient warehouse management is crucial for Malaysian Micro, Small, and Medium Enterprises (MSMEs) aiming to thrive in a competitive market. By optimizing inventory management and streamlining logistics, MSMEs can enhance operational efficiency, reduce costs, and improve customer satisfaction.
Challenges in Warehouse Management for MSMEs
Limited Space and Resources
Many MSMEs operate within constrained budgets and physical spaces, making warehouse optimization challenging. To address this, businesses can implement vertical storage solutions, utilize mezzanine flooring, and adopt lean inventory practices to maximize available space. Implementing an efficient inventory management system can also help in tracking stock levels accurately, ensuring optimal use of space.
Lack of Skilled Labor
The shortage of skilled labor can hinder efficient warehouse operations. To mitigate this, MSMEs can invest in employee training programs focused on warehouse management best practices. Additionally, adopting user-friendly inventory management software can reduce the dependency on specialized skills, allowing staff to manage operations more effectively.
Inefficient Inventory Systems
Relying on manual inventory tracking can lead to errors and inefficiencies. Implementing cloud-based inventory management software enables real-time tracking, reduces human errors, and enhances decision-making. For instance, solutions like 8Stock offer comprehensive inventory management features suitable for small businesses.
Opportunities and Solutions
Technology Adoption
Integrating technology into warehouse operations presents significant opportunities for MSMEs. Adopting Warehouse Management Systems (WMS) and automation tools can streamline processes, improve accuracy, and reduce labor costs. Open-source ERP solutions like inoERP provide customizable modules for inventory and warehouse management, catering to the specific needs of small businesses.
Market Growth and E-commerce
The rise of e-commerce offers MSMEs avenues for growth. By optimizing fulfillment strategies, businesses can meet the increasing demand efficiently. Utilizing inventory management platforms that integrate with e-commerce platforms ensures seamless order processing and inventory synchronization. For example, 8Stock order management (now part of Uniqbe) provided such integrations, enhancing operational efficiency for small businesses.
Regulatory Compliance
Ensuring compliance with local regulations is vital for MSMEs to avoid penalties and maintain reputation. Implementing inventory management software with features like automated reporting and audit trails can assist in adhering to regulatory requirements. Cloud-based solutions also offer real-time updates, ensuring that businesses remain compliant with evolving standards.
How to Arrange Stock for Faster Picking
1. ABC Analysis
This method categorizes stock into three groups based on demand:
- A-items: High-demand products are placed at eye level for easy and quick access.
- B-items: Medium-demand products are stored slightly lower or higher.
- C-items: Low-demand products are placed in less accessible areas to save space.This approach ensures that frequently picked items are always within reach, reducing time wasted on retrieval.
2. Batching Similar Items
Grouping related items together simplifies the picking process. For instance, similar SKUs like different sizes or colors of the same product should be shelved near each other. This reduces the time spent moving between aisles and shelves, and helps avoid mistakes during order picking.
3. Clear Labeling & Signage
Properly labeled shelves and bins are crucial for avoiding errors. Every SKU should have a visible, easy-to-read label. Use barcodes or QR codes for digital inventory management and speed up the picking process. Clear signage in aisles and sections helps pickers navigate the warehouse efficiently.
4. FIFO System (First In, First Out)
This strategy ensures older stock is always retrieved first, reducing the risk of expiration, obsolescence, or damage. The items that were stocked first should be easily accessible, so they’re picked before newer stock. FIFO is especially useful for perishable goods.
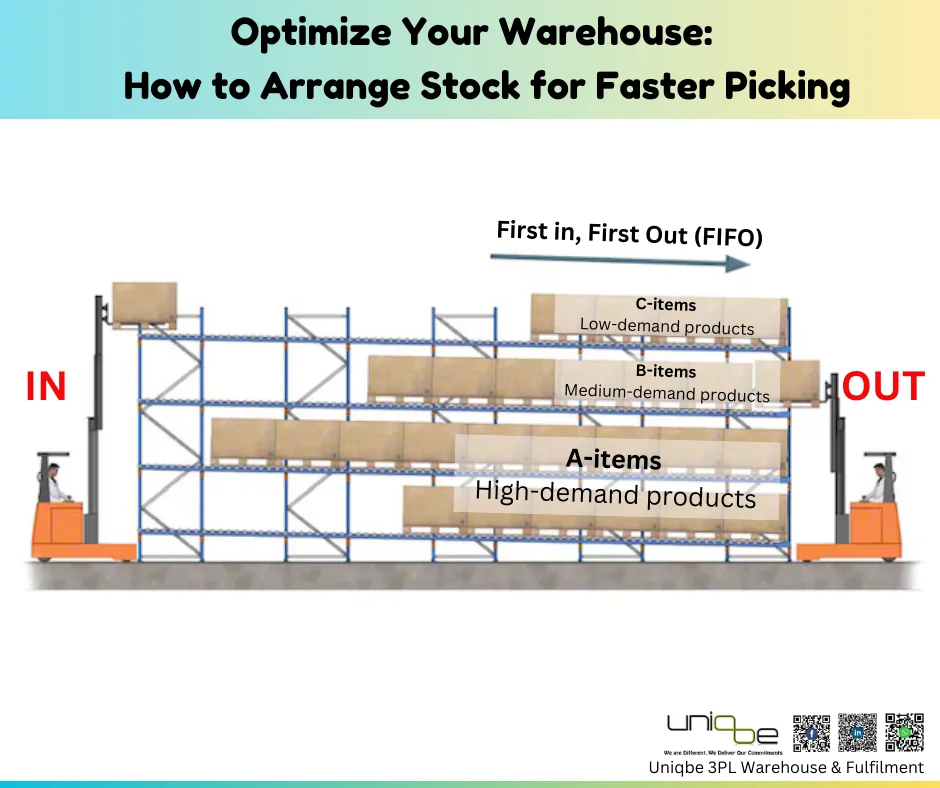
5. Dynamic Slotting
Instead of keeping products in fixed locations, dynamic slotting involves regularly adjusting stock placement based on changing demand trends. Fast-moving products can be relocated to prime spots for a certain period, while slow-moving items are shifted out. This system ensures the most efficient use of space and reduces picking time for high-demand products.
By implementing these strategies, you can optimize stock placement, increase order processing speed, and improve overall warehouse efficiency.
Best Practices for MSMEs
Data-Driven Decision Making
Leveraging data analytics enables MSMEs to make informed decisions regarding inventory levels, order quantities, and demand forecasting. Cloud-based inventory systems provide real-time data, facilitating accurate analysis and timely decision-making.
Continuous Improvement
Regularly reviewing warehouse processes and seeking areas for improvement fosters a culture of continuous enhancement. Implementing feedback loops, conducting regular audits, and staying updated with industry trends can lead to ongoing operational improvements. Utilizing inventory management software that offers customizable reporting can aid in identifying inefficiencies.
Collaboration and Outsourcing
Collaborating with third-party logistics providers can be beneficial, especially when scaling operations or managing seasonal demand fluctuations. Outsourcing certain logistics functions allows MSMEs to focus on core business activities while ensuring efficient warehouse operations. Evaluating the cost-benefit ratio and selecting partners with compatible systems can lead to successful collaborations.
Ready to take your warehouse efficiency to the next level?
Contact us today to learn how our 3PL fulfillment services can streamline your inventory management and boost your operations.